There are diverse types of medical plastic polymers, and every plastic grade comprises distinct characteristics that inform they are respective for specific medical devices. Here are some of the commonest medical plastics for medical devices and their properties.
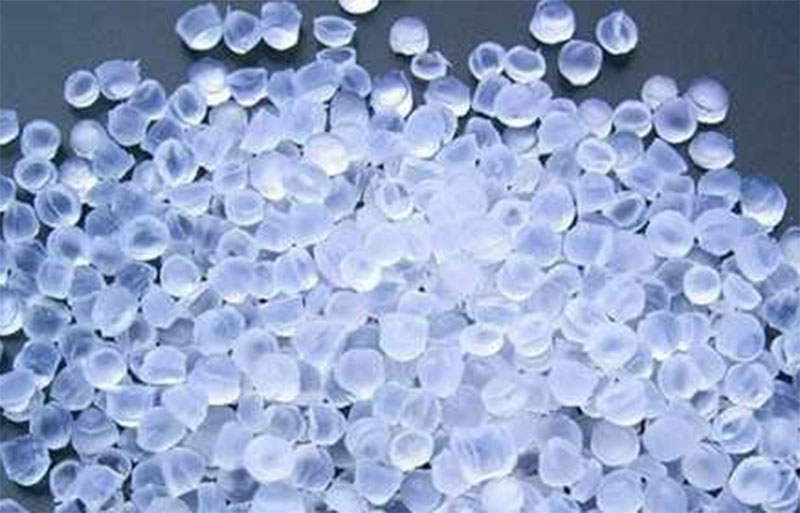
- Polycarbonates(PC)
As the name suggests, polycarbonates (PC) comprise carbonate groups in their chemical structure. These thermoplastic polymers are highly praised and applied for their high impact and thermal resistance. They also provide good toughness, UV protection, durability, and electrical and optical properties.
Aside from this, polycarbonate sheets are pliable or workable into various shapes at room temperature without cracking. Due to their high heat resistance, they do not deform when exposed to high temperatures or steam. As such, experts often apply polycarbonate sheets for medical panels and signage.
- Polypropylene(PP)
This medical plastic grade is often applied for many applications where resistance to high temperatures remains vital. This is because polypropylene-produced medical plastic parts can undergo extreme steam sterilization and maintain decent durability after processing. Moreover, it is recyclable and more cost-effective than other medical plastic polymers.
Polypropylene’s easy moldability into various shapes as well the stability to acids, bases, and other solvents, also contributes to its uniqueness and justifies its widespread use. Hence, most manufacturers use this plastic grade to produce non-absorbable sutures, plastic containers, clear bags, prescription bottles, disposable syringes, connectors, and finger-joint prostheses.
- Polyethylene(PE)
This thermoplastic material is durable, tough, cost-effective, and suitable for various plastic processing methods. Its high resistance to impact and chemical and low moisture absorption properties makes it an ideal choice for manufacturing medical devices. Additionally, it is biologically inert and does not retain harmful organisms.
Polyethylene is often used in the medical field for fabricating medical implants because it is biocompatible and does not decompose in the body over time. Similarly, healthcare professionals can also subject these parts to various sterilization techniques and highly concentrated cleaning agents.
- Polyvinylchloride(PVC)
This plastic grade is also called PVC plastic. PVC is available in diverse forms, but thermoplastic grades with high thermal stability, corrosion resistance, and flame retarding features remain the most used plastic polymer in the medical industry.
More so, this plastic material is usually molded to fabricate rigid or flexible medical parts depending on the amount of plasticizer added to produce the required hardness. Manufacturers often apply PVC to make catheters, feeding tubes, and infusion bags for nutrients and dialysis fluids.
- Acrylonitrile Butadiene Styrene(ABS)
This plastic grade, also known as ABS plastic for short, is a thermoplastic copolymer that serves as an exceptional substitute for metal parts of medical devices. ABS plastic is rigid, durable, and provides an appealing aesthetic quality that is perfect for the medical field due to its easy coloration. Aside from this, it can undergo various molding processes to form different medical plastic parts.
Further, ABS can withstand medical sterilization techniques like gamma radiation or chemical sterilant such as ethylene oxide (EO). Hence, ABS plastic sheets are ideal for manufacturing non-absorbable sutures, tendon prostheses, tracheal tubes, and other drug-delivery systems.
- Polystyrene(PS)
This plastic material is also used for a wide range of medical applications due to its ease of sterilization. Its optical properties make it suitable for manufacturing parts such as test tubes, diagnostic tools, Petri dishes, casing for test kits, tissue culture trays, and other medical devices. - Polyethylene Terephthalate Glycol (PETG)
PETG is a transparent, durable, machinable, and thermoplastic polymer widely used for medical applications. Typically, it is ideal for medical use because it can withstand sterilization procedures, including radiation and liquid chemicals, without fading.
PETG is also applied for manufacturing food containers. Thus, it is usually the ideal choice of plastic container in the food preparation zone of hospitals and clinics, but you may also find PETG sterilization trays in some hospitals.
- Polymethyl Methacrylate(PMMA)
It is also called acrylic. This plastic material comprises specific properties similar to glass. As such, the medical grade plastic can reflect and transmit beams of light, and this inherent characteristic makes it an excellent choice for fabricating endoscopic implants.