ABS stands for Acrylonitrile Butadiene Styrene. This plastic material comprises three monomers that make up its name. Each of these monomers contributes its properties to the polymer plastic to give it a wide range of properties.
The properties the plastic possesses include chemical resistance, hardness, and heat resistance contributed by acrylonitrile. Other properties include impact resistance and toughness (bestowed by butadiene) and strength and gloss contributed by styrene. Despite its wide range of features, it is relatively one of the cheapest plastics to purchase. Also, it is one of the easiest plastics to use in injection molding due to its ease of processability.
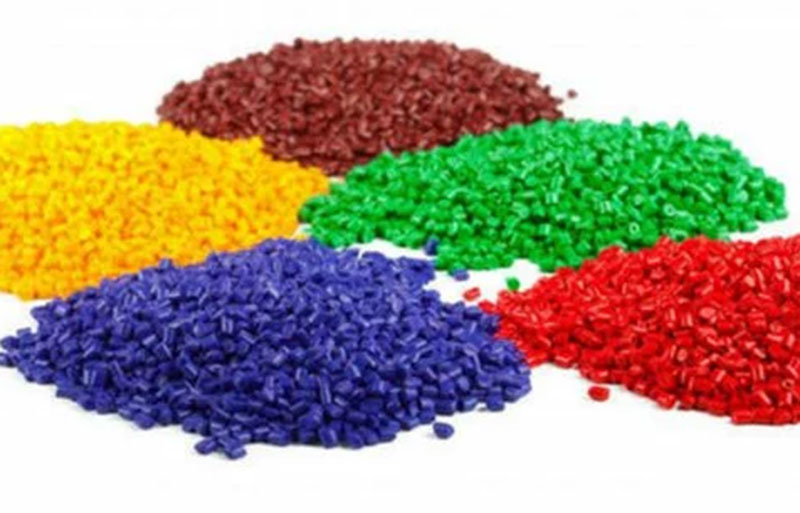
Despite its acclaimed strength and toughness, this strong plastic isn’t so impervious to UV light. Hence it has limited outdoor use. However, part manufacturers have found ways to manipulate the properties of this plastic to withstand UV light by using various additives and fillers such as acrylic, glass, and stainless steel fibers. These additives alter the properties of the plastic and further enhance its uses for various applications.
These properties and potential for manipulation make ABS the most widely used polymer in the injection molding process.