Zinc alloy die castings are alloys composed mainly of non-ferrous metal zinc and incorporating other metal elements. Common alloying elements include aluminum, copper, magnesium, cadmium, lead, titanium, etc. Compared with other die-casting methods, high pressure and high speed are particularly evident in zinc alloy die-casting. Why is the use of zinc alloy die castings so widespread?
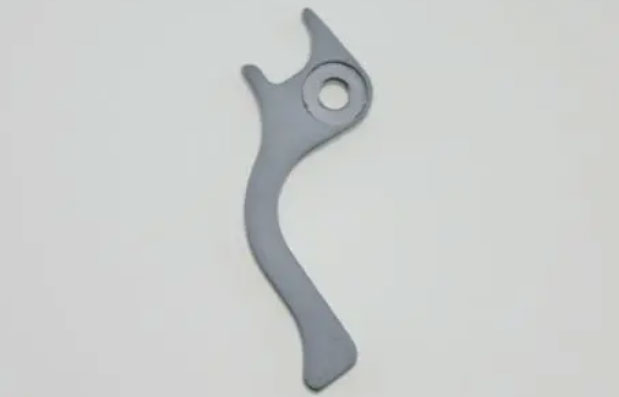
- Because zinc alloy has a low melting point and can melt at 385 ℃, it is easier to form than other alloy die-casting; Good fluidity, does not absorb iron during melting and die-casting, does not corrode the mold, and does not stick to the mold; These characteristics make zinc alloys highly productive.
- Good casting performance, capable of die-casting complex and thin-walled parts with a smooth surface.
- Easy to process, capable of various surface treatments, with a beautiful appearance.
- Due to the precise size of zinc alloy molds, the products produced by die casting only require a small amount of processing to be directly used, improving the efficiency of alloy utilization and reducing a large amount of processing equipment and time. So the cost-effectiveness is very high.
- Zinc alloy is corrosion-resistant in the atmosphere, and residual waste is easy to recover and remelt for secondary utilization.
So the application fields of zinc alloy die castings are becoming increasingly wide. Its mass production, casting performance, high cost-effectiveness, and other advantages have made zinc alloy die casting products occupy a place in the die casting industry.