Vacuum thermoforming is a type of thermoforming that involves using vacuum pressure to form a plastic sheet into a specific shape. This process is commonly used in the production of packaging, trays, and other plastic products.
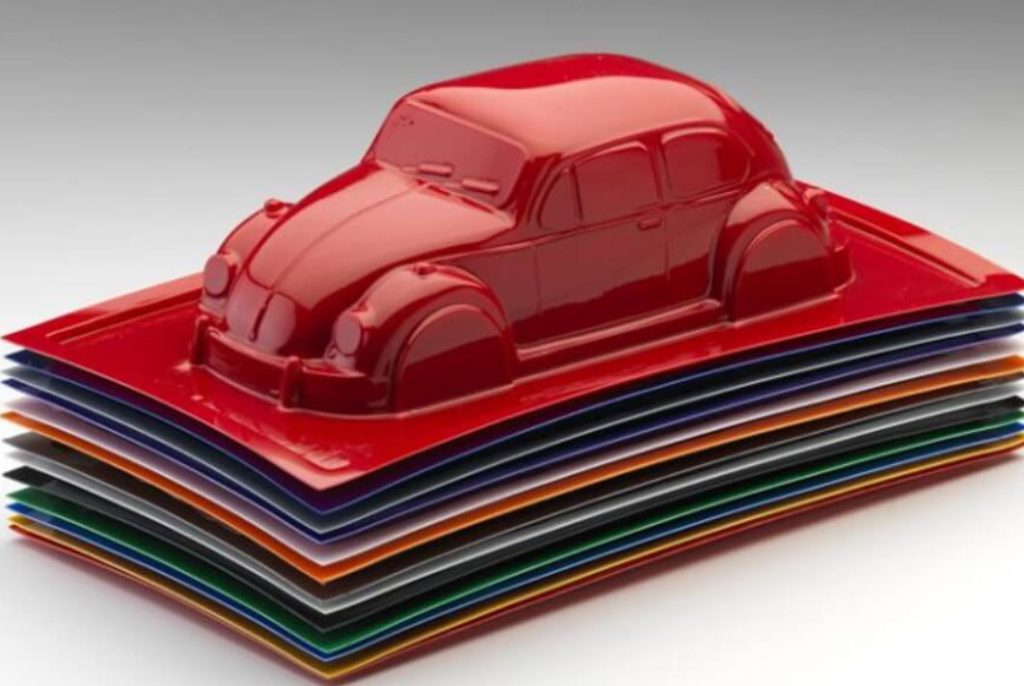
The vacuum thermoforming process can be broken down into four main steps: heating, forming, cooling, and trimming. First, the plastic sheet is heated to a temperature where it becomes pliable. Then, it is placed over a mold and vacuum pressure is applied to form the sheet into the desired shape. Next, the formed part is cooled and trimmed to its final size and shape.
One of the advantages of vacuum thermoforming is its ability to produce parts with consistent wall thickness. This is because the vacuum pressure helps distribute the plastic evenly over the mold. Additionally, it is a cost-effective process for producing large quantities of parts.
Vacuum thermoforming is also a relatively fast process, with cycle times ranging from seconds to minutes depending on the size and complexity of the part. This makes it an ideal choice for industries where speed and efficiency are important.
In conclusion, vacuum thermoforming is a widely used manufacturing process that offers consistency, cost-effectiveness, and speed. Its applications are diverse and continue to expand as new materials and techniques are developed.