What are the common problems in overmolding? Overmolding, also known as secondary injection molding, requires the plastic raw materials to be molded in the mold, the formed parts to be taken out, and then placed in the glue packaging mold for injection molding again. The front and back processes of this process are closely intertwined, and a slight lack of attention may lead to the occurrence of defective problems.
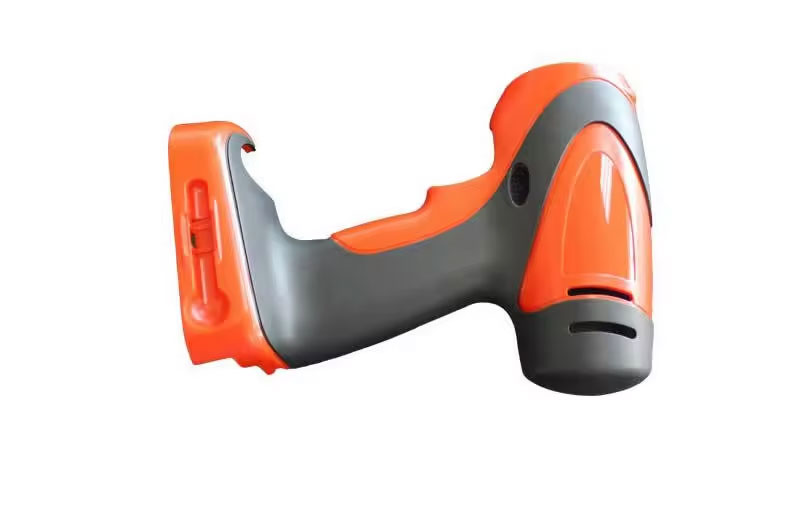
- When there is a deviation in the size of the injection molded part, the injection molding process usually involves first injecting hard rubber and then injecting soft rubber. Soft rubber is usually used to meet appearance requirements, so the size requirements are not strict. But in general, soft glue does not shrink, while hard glue shrinks. If the second injection molding does not meet the time requirements after the first injection molding is completed, it is easy to cause dimensional deviation;
- The package is not tight, and the two materials are tightly wrapped. The roughness of the mold surface needs to be considered. Therefore, when debugging injection molded parts, it is necessary to turn on the machine for debugging to prevent the injection molded products from sticking to the mold or plugging materials. In other times, try to avoid using release agents as much as possible.
- The molding cycle is too long, and this type of problem often occurs in plastic injection molding. The main reason is that it requires two rounds of injection molding, so the efficiency is slightly lower than that of two-color injection molding.
The above are common questions about overmolding , If you have any other technical questions about plastic injection molding, please feel free to contact our over 20 year mold injection molding team by phone to learn more technical solutions and communicate with us!