The design of continuous molds mainly depends on how the product or component passes through them. A challenging stage in progressive mold (continuous mold) design is rotating parts along the metal strip. In most cases, rotating components to optimize materials is usually the only option. In other cases, you need to compromise between component rotation and cam angle. This will directly affect your continuous mold and tool costs as well as design.
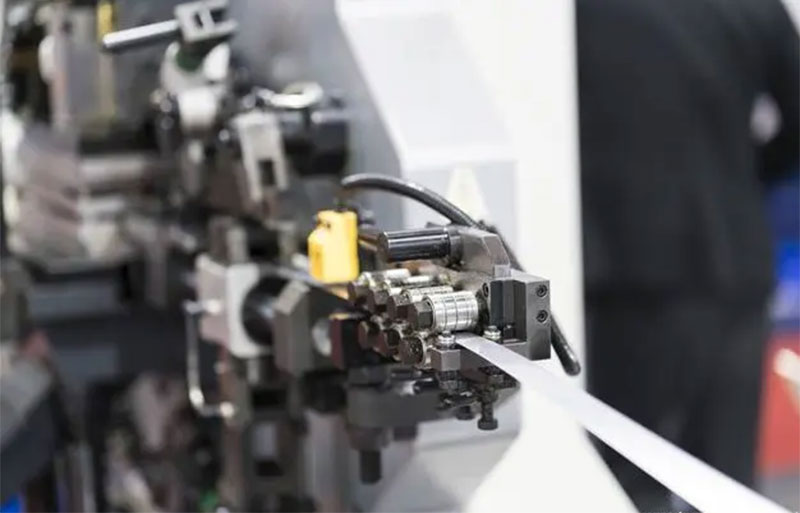
Another factor that determines the direction of the component is the lift required to transport the strip from one stage to another. However, you can design your continuous mold and tools to make the parts rotate well, so you don’t need to lift them. Alternatively, you can eliminate the need for elevators when molding tools upwards. If the direction of the part formation is opposite, you can make subtle adjustments in material usage optimization, tool complexity, and excessive improvement.
Another factor to consider when shortening the material feed is the rotation of the components. If the feed is shorter, there will be fewer issues and faster running speed. If there is a significant difference between the width and length of your components, your design will be more effective if your progressive mold has shorter leads.