The treatment technology that uses modern technology to change the composition, structure, and properties of the material surface and sub surface layer of die-casting molds is called surface modification technology.
- Electrochemical conversion
The technology of forming an oxide film on the surface of parts under the action of electrolyte solution and external current is called electrochemical modification technology. Electrochemical conversion modification technology is often referred to as anodizing or anodizing in engineering. Recently, a major exhibition of electrochemical conversion technology is micro arc plasma anodizing, which can significantly improve surface hardness or form new colored decorative film layers, and has good applications in the mold industry. - Surface formation and strengthening
By using techniques such as shot peening, extrusion, laser shock, rolling, ultrasonic shock, vibration shock, and high-pressure jet, the surface layer of the material undergoes elastic-plastic deformation, introducing residual compressive stress and resulting in changes in microstructure, in order to improve the corrosion resistance of the material and enhance the stability and durability of die casting mold components. - Surface phase transformation strengthening
The surface of the die-casting mold is rapidly heated using electron beams, laser beams, etc., to form new phase transition zones and surface strengthening amounts on the surface and subsurface, resulting in a special performance of fine structure and strengthening phases.
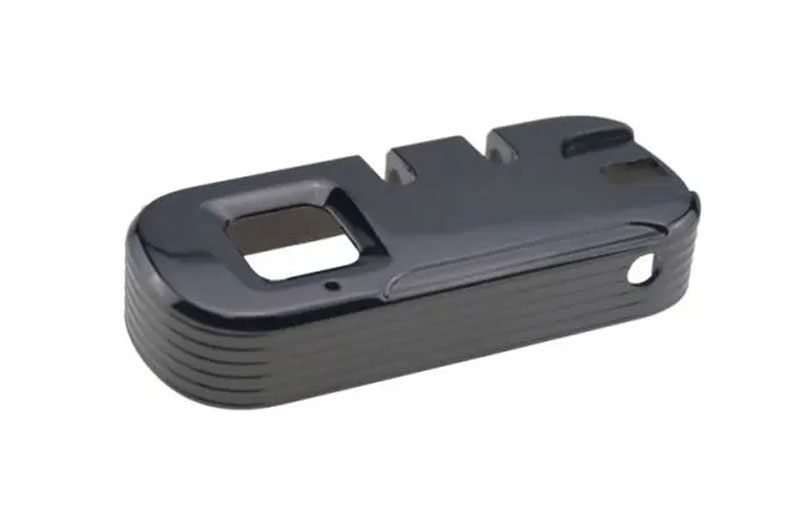
- Ion implantation
The ions ionized by the vacuum system are accelerated under high voltage and directly injected into the material surface to form a very thin ion implantation layer, which changes the composition and structure of the material surface and its surface properties. - Inorganic coating technology
Coating technology mainly refers to the use of coatings (paint, paint, pigment, diluent) to endow the surface of die casting mold components with special protection, decoration, flame retardancy, temperature indication and other functions.
Inorganic coating technology is to form an inorganic coating or surface facial mask on the metal surface. Inorganic coatings or surface facial mask have specific chemical composition, structure and morphology, which can endow the substrate and coating system with new properties or functions.
- Surface alloying (diffusion infiltration)
Depositing metal or non-metal on the surface of die casting, infiltrating into the surface through diffusion, changing the chemical composition and phase structure of the mold surface, in order to improve the usability of the material surface. - Chemical conversion
Put the die-casting mold components into a certain chemical solution medium to form a passive compound film layer on their surface, in order to improve the performance of the mold surface. The commonly used passive compound film layers in engineering mainly include chromate passivation film, acid salt passivation film, oxalate passivation film, and blueing of the surface of mold components. In addition, in engineering applications, surface roughness reduction processes (such as polishing, rolling, etc.) and surface coloring are often classified as surface modification processes such as chemical conversion.