Extrusion molding is an efficient, continuous, low-cost, and wide-adaptability molding method. It is an early technology in polymer material processing. After more than 100 years of development, extrusion molding is the molding method with the most varieties, the most changes, high productivity, strong adaptability, wide application, and the largest output in the field of polymer processing. Extrusion molding is one of the most important forms of plastic material processing. It is suitable for most plastic materials except some thermosetting plastics. About 50% of thermoplastic plastic products are completed by extrusion molding. At the same time, it is also widely used in the molding of chemical fibers, thermoplastic elastomers and rubber products. The extrusion molding method can produce continuous products in various forms such as pipes, rods, sheets, profiles, wire and cable sheaths, monofilaments, etc. It can also be used for mixing, plasticizing, granulating, coloring and blending modification of polymer materials. In addition, based on extrusion molding, extrusion-blow molding technology and extrusion-stretching molding technology combined with blowing, stretching and other methods are important methods for manufacturing films and hollow products.
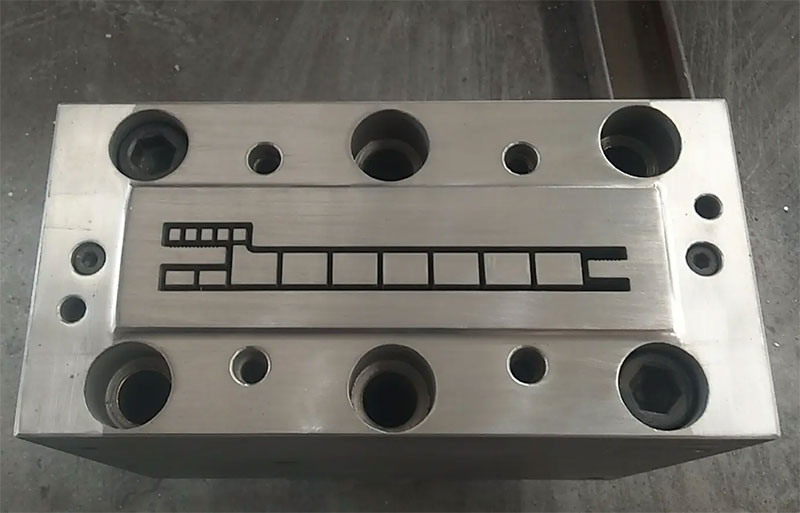
Extrusion molding, also known as extrusion molding or extrusion molding, mainly refers to a molding method that uses the extrusion effect of a screw or a plunger to force the heated and molten polymer material through the die head under pressure to form a continuous profile with a constant cross-section. The extrusion molding process mainly includes the processes of feeding, melt plasticization, extrusion molding, shaping and cooling.
The extrusion process can be divided into two stages: the first stage is to plasticize the solid plastic (that is, turn it into a viscous fluid) and pass it through a specially shaped die under pressure to become a continuum with a cross-section similar to the die shape; the second stage is to use appropriate methods to make the extruded continuum lose its plastic state and turn it into a solid to obtain the desired product.
According to the different ways of plasticizing plastics, the extrusion process can be divided into two types: dry method and wet method. Dry plasticization is to turn plastic into melt by heating. Plasticization and pressurization can be carried out in the same equipment, and the shaping process is only simple cooling. Wet plasticization is to soften the plastic fully with solvent, so plasticization and pressurization must be divided into two independent processes, and the shaping process must use more troublesome solvent removal, and the recovery of solvent must also be considered. Although wet extrusion has advantages in uniform plasticization and avoiding excessive heating of plastics, due to the above disadvantages, its scope of application is limited to the extrusion of cellulose nitrate and a few cellulose acetate plastics.