1. The surface of die-casting parts is a dense surface layer, approximately 0.05mm to 0.1mm. Below the surface is a loose and porous structure. Therefore, when polishing and polishing, do not throw off all the surface layer to expose the loose bottom layer, otherwise electroplating is very difficult and will reduce the corrosion resistance of the product.
2. Die-casting parts change from a molten state to a solid state during the die-casting process. Due to the different solidification points during cooling, segregation often occurs on the surface of die castings. Therefore, during pre-treatment, do not use strong alkali and strong acid for degreasing and etching, otherwise it is easy to cause peeling and bubble formation.
3. The shape of zinc alloy die castings is generally complex, and a solution with good dispersion and coverage ability should be used for electroplating. To prevent the displacement of zinc on metal with positive potential at concave or masked areas, which may result in poor adhesion, the pre coating should choose a plating solution with good dispersion and coverage ability.
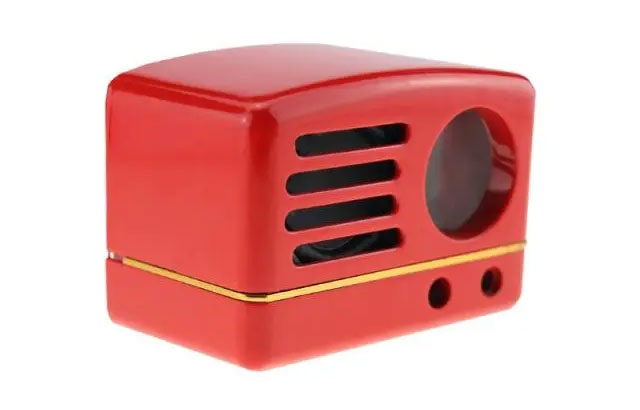
4. The coating used should be bright, avoiding polishing processes or reducing polishing workload as much as possible. On the one hand, due to its complex shape, it is not easy to polish, and on the other hand, it can also ensure the thickness of the coating and ensure quality.
5. If the first layer of coating is made of copper, its thickness should be slightly thicker, because when copper is plated on the surface of the zinc alloy, copper diffuses into the zinc and forms a brittle copper zinc alloy intermediate layer. The thinner the copper layer, the faster the diffusion occurs, so the thickness of copper should reach at least 7 μ M or thicker.
6. The multi-layer chromium plating layer is a cathodic protection coating of zinc alloy, so the coating must have a certain thickness to ensure that there are no pores in the coating. Otherwise, due to the negative electrode potential of zinc alloy, it is easy to produce white powdery corrosion products of alkaline zinc carbonate in humid air. It is necessary to choose an appropriate coating thickness based on the product’s usage conditions.
7. If the die-casting process is not suitable or the die-casting mold design is unreasonable, resulting in cold lines, shrinkage holes, porosity, etc. on the die-casting surface, even if measures are taken in the electroplating process, satisfactory coatings are often not obtained.