Injection molding temperature: Excessive injection molding temperature may cause problems such as deformation and shrinkage of the product, while low temperature can make the surface of the product rough and internal voids. Therefore, the appropriate injection molding temperature should be selected based on the properties of TPE material and product requirements.
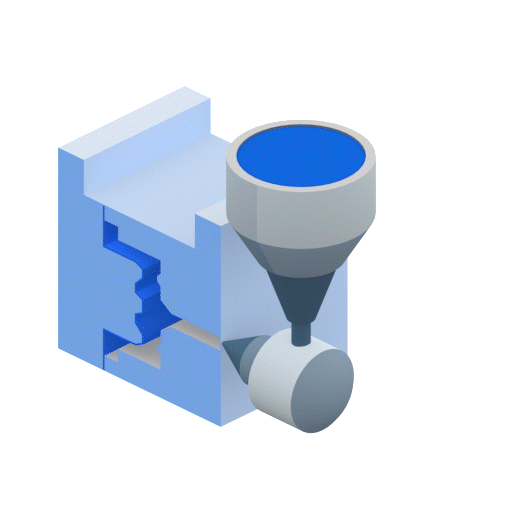
Injection pressure: Insufficient injection pressure may lead to problems such as incomplete filling and surface depression of the product, while excessive pressure can cause phenomena such as flash and overflow of the product. The appropriate injection pressure should be adjusted according to factors such as product structure and mold design.
Holding time: Insufficient holding time can cause internal voids and unstable dimensions in the product, while prolonged holding time can lead to deformation, cracking, and other issues. Appropriate holding time should be set according to the characteristics of TPE material and product requirements.
Cooling time: Insufficient cooling time can cause deformation and cracking of the product during demolding, while prolonged cooling time can affect production efficiency. Reasonable cooling time should be set according to factors such as product thickness and the mold structure of injection molding.