Magnesium alloy is an alloy composed of magnesium and other metals, and is currently the lightest structural metal material known. Its density is only a quarter of steel and two-thirds of aluminum. Due to its lightweight, high strength, heat resistance, corrosion resistance and other characteristics, magnesium alloys are widely used in aerospace, electronic communication, medical equipment and other fields. In recent years, with the increasing demand for lightweight automobiles, magnesium alloys have also shown great potential and prospects in the automotive industry.
But, the development of magnesium alloy automotive die casting industry faces the following current situation and challenges:
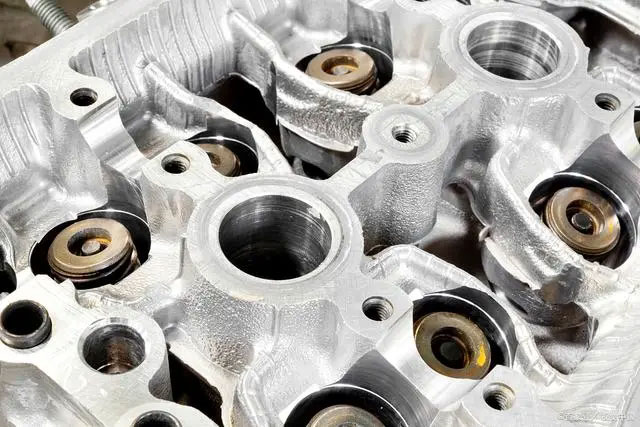
The demand for lightweight continues to grow. Lightweight refers to reducing the weight of a car as much as possible while ensuring its performance and safety, thereby reducing fuel consumption and emissions, and improving power and handling. Lightweighting is one of the important means to address energy crisis and environmental issues, as well as a key factor in enhancing the competitiveness and market share of automobiles. With the national policy guidance on energy conservation and emission reduction and the increasing awareness of green travel among consumers, the demand for lightweight transportation will continue to grow. Especially in the field of new energy vehicles, due to issues such as low battery energy density, high weight, and high cost, lightweighting is of great significance for improving range, reducing costs, and increasing passenger space. According to the “Energy saving and New Energy Vehicle Technology Roadmap 2.0”, by 2035, the lightweighting coefficient of China’s new energy vehicles will be reduced by 35% compared to 2020.
Secondly, magnesium alloys have excellent performance. Magnesium alloy, as a lightweight material, has significant advantages such as weight reduction, excellent seismic and noise reduction, and good die-casting performance. Compared to steel and aluminum alloy, magnesium alloy has a lower density, which is one-quarter of steel and two-thirds of aluminum alloy, respectively. Therefore, while maintaining the same volume, automotive parts made of magnesium alloy can achieve a weight reduction of 25% -75%. In addition, magnesium alloys have low elastic modulus and high attenuation coefficient, which can effectively absorb and dissipate vibration and noise, improving the comfort and safety of automobiles. Magnesium alloys also have good die-casting performance, which can produce complex shapes and structures, reduce subsequent processing and assembly steps, and lower production costs and time.
Thirdly, the price of magnesium alloys has decreased. The price of magnesium alloy is an important factor affecting its application in the automotive industry. Due to the high chemical activity, easy oxidation, flammability and explosiveness of magnesium alloys, special measures and equipment are required in their production process, resulting in high production costs. In addition, due to the low application proportion of magnesium alloys in automobiles, their market size and industrial chain are not yet perfect, which also makes their prices relatively high. However, with technological advancements and market expansion, the price of magnesium alloys is showing a downward trend. According to data from a consulting firm group, the average price of magnesium alloy AZ91D in China was 23700 yuan/ton in February 2023, a decrease of 8.7% compared to the same period in 2022; The average price of domestic aluminum alloy ADC12 is 19000 yuan/ton, an increase of 9.2% compared to the same period in 2022. Therefore, the price ratio of magnesium alloy to aluminum alloy decreased from 1.5 in February 2022 to 1.24 in February 2023, indicating that magnesium alloy has a higher cost-effectiveness compared to aluminum alloy.
The fourth is the expansion of the application of magnesium alloys. With the increasing demand for lightweight and the advantages of magnesium alloy performance and price, the application scope and quantity of magnesium alloy in automobiles are constantly expanding. At present, multiple domestic and foreign automobile brands have adopted magnesium alloy components, mainly focusing on internal structural components such as instrument panel brackets, seat frames, steering wheel brackets, airbag covers, and steering columns. According to data from a consulting firm group, the average magnesium alloy consumption per bicycle in China is expected to reach 10 kilograms in 2023, an increase of 66.7% compared to 2022; The average magnesium alloy usage per bicycle in the North American market is expected to reach 18 kilograms, an increase of 20% compared to 2022. It is worth noting that in the field of complex large structural components, such as powertrain housings, gearbox housings, etc., industrial breakthroughs have also been achieved and there is hope for large-scale applications. These components not only require high material performance, but also high process technology, and their single piece value is also high, so their contribution to lightweighting is greater. For example, Wanfeng Aowei provided SAIC Volkswagen with the world’s first magnesium alloy gearbox housing, which weighs only half of aluminum alloy and achieves a weight reduction effect of 50%.
In summary, the current situation and challenges of the magnesium alloy automotive die casting industry are: continuous growth in lightweight demand, excellent performance of magnesium alloys, decrease in magnesium alloy prices, and expansion of magnesium alloy applications. These factors have jointly promoted the development of the magnesium alloy automotive die casting industry, but there are also some problems and difficulties that need to be solved. For example, the oxidizability of magnesium alloys makes them prone to corrosion and ignition in high temperature and humid environments, affecting their service life and safety; The cost of magnesium alloys is still higher than traditional steel and aluminum alloys, which limits their competitiveness in the low-end market; The process difficulty of magnesium alloys is high, requiring high-level design, manufacturing, and testing capabilities. Currently, there is still a certain technological gap between China and foreign countries. Therefore, the magnesium alloy automotive die-casting industry should strengthen technological innovation, reduce costs, improve quality, and expand the market to adapt to the trend and demand of automotive lightweighting.